Source Capture for Spin-Welding
Continuous-Duty Vacuums were needed for the recovery of welding dust from a spin welding application.
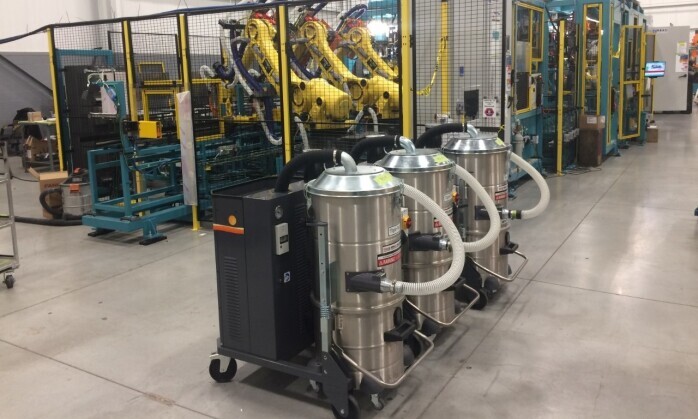
The Problem
A Systems Integrator approached Controlled Air Design to provide a solution for a continuous spin welding application within a robotic cell. The process of spin welding consists of generating heat by rotating friction to weld thermoplastic parts with circular joints. The spin welding machine applies force axially while rotating one part against its stationary mate. The resulting friction generates heat that fuses the parts together. Once rotation stops, the material cools and solidifies, forming a welded assembly. For cases where the parts must be oriented in a particular manner with respect to each other, the welder stops the rotation at a precise angular orientation. The Spin-Welding process generates a modest amount of inert dust that would otherwise go airborne.
The Solution
We recommended a continuous-duty vacuum. Equipped with continuous-duty vacuums have “regen” or regenerative induction motors. These are the old-fashioned production motors that have a primary winding that induces a current in a secondary winding. We recommend this type of motor if you are running non-stop for 1 or 2 shifts. The vacuum hose was directly connected to a pickup point on the Spin-Welder. The connection hoses used were highly flexible to allow movement.
The vacuum had been in use for about 6 weeks when the plant manager reported improved efficiency and returned clean breathable air back into the work space as the vacuum filters particles down to .3 micron @ 99.97% efficiency. The plant manager also reported that the solution we provided increased productivity. We are happy to say that they have since become a valuable repeat client of ours.
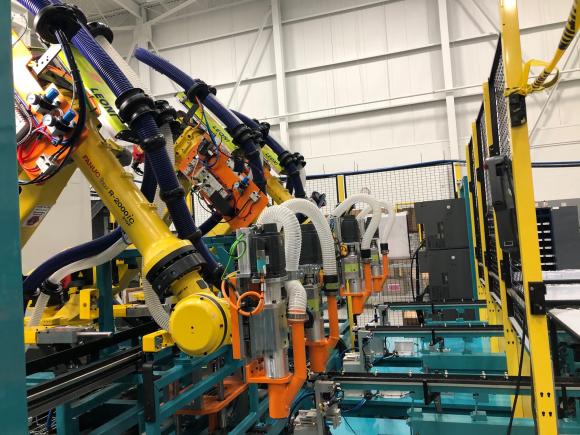