Sticky Soldering Fumes
U.S. soldiers will get new body armor for the first time in a decade, starting this summer.
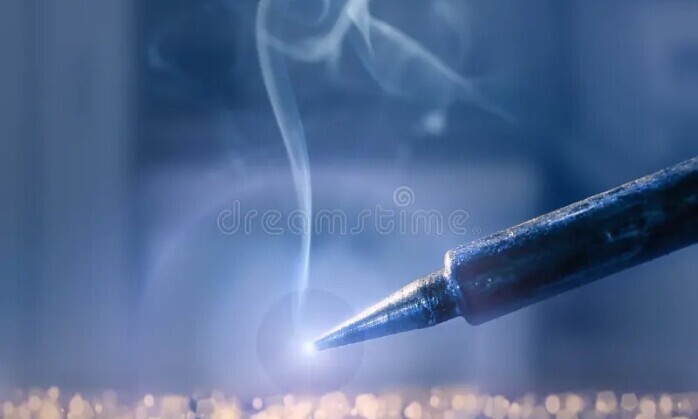
The Problem
We were approached by an army base to provide source-capture from 40 soldering stations. These stations were working around the clock on a time-sensitive plan to manufacture the new Modular Scalable Vest. Each station was emitting a sticky fume created by melting polyester and metal alloys; these fumes usually overwhelm conventional filtration devices. As such, we had to think of a solution that would allow for proper filtration- but one that would not cause a drop in productivity from workers having to clean filters.
The Solution
Controlled Air Design created a system where “Source-Capture” filtration allowed Army technicians to solder around the clock without stopping to clean filters. We suggested our PDB-1500 with a custom filtration solution to absorb the sticky fumes into a hood placed 6”–8” away from the soldering iron. The fumes passed through 2 stages of pre-filtration and into a 24”x24”x12”, 95% Glass-Filled ASHRAE Filter (for sticky fumes), and then into 56 lbs.of Activated Carbon (for odors), and finally a HEPA Final-Filter (for particulate). The Custom Fume Booth’s exhaust produced breathable clean air.
By offering this solution, we were able to ensure that productivity was maximized while maintaining high safety standards.
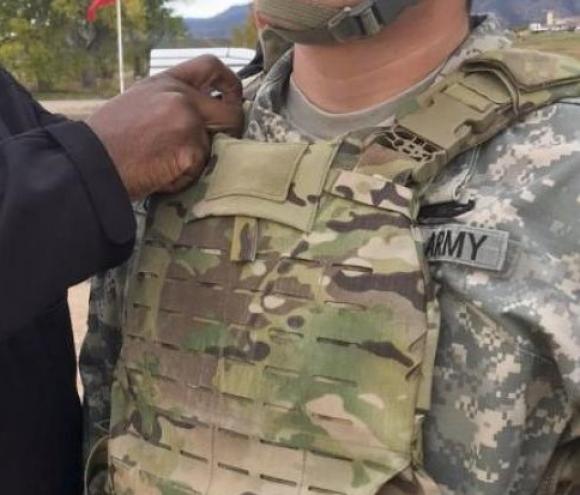