Static-Free Vacuum Cleaners
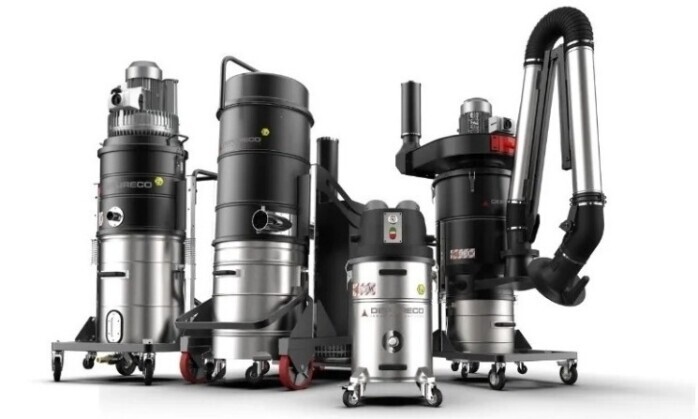
NFPA 660-Compliant Electric Vacuums for ST1 Dusts in ORDLOC
Vacuum Cleaners for NFPA 660
BL-PRO ATEX HEPA 110V
H14 HEPA Captures 99.995% of particles down to 0.18 microns
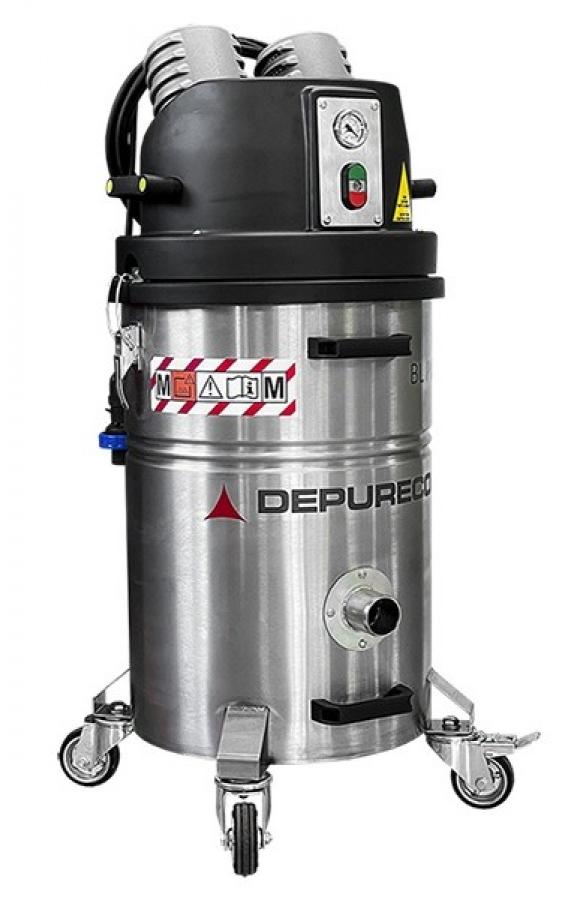
BL-PRO ATEX HEPA 110V features a potent brushless motor, antistatic polyester certified Class M, plus an optional HEPA 14 filter can be installed.
All the collected debris accumulates within an 11 gal capacity container crafted from AISI 304 stainless steel.
For most XP powder housekeeping vacuuming applications in ordinary locations (ORDLOC) The BL-PRO is all you need.
This vacuum is usually in stock for quick delivery!
Click HERE to see a brochure
Specifications:
Motor | Primary Filter | Machine |
---|---|---|
Motors | Type Brushless Motor | Filter Type Star filter | Dimensions 20.32x21.46 in |
Voltage | Frequency 120 | 60 V|Hz | Class EN 60335-2-69 M Class | Height 41.33 in |
Maximum Air Flow 129 CFM | Media Antistatic Polyester | Weight 83.78 lb |
Noise Level-(EN ISO 3744) 72 dB(A) | Surface Area 930 in² | Bin Capacity 11 gal |
Power 1.5 - 2 HP | Spark-Safe Filter | |
Vacuum Continuous Use 92 in H2O | ||
Inlet 2 Ø in |
BL-45 ATEX Z22
Compact Stainless Vacuum with a high-performance Brushless motor
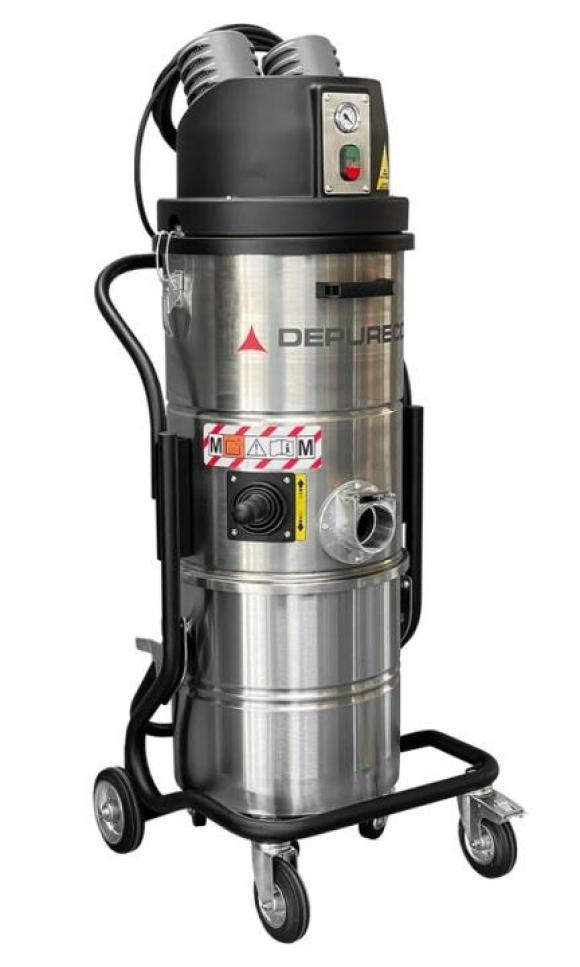
The BL 45 Z22 is a compact model with a high-performance Brushless motor, it provides powerful suction and silent operation. It features a large surface filter certified as class M, efficiently capturing particles as small as 1 micron.
An optional absolute filter H14 that is captures 99.995% of particles down to 0.18 microns is available for removing finer dust.
The filter chamber is made from AISI 304 stainless steel, ensuring durability. Cleaning the filter is easy with a robust manual shaker.
Collected material is deposited in a 12-gallon AISI 304 stainless steel container for durability and maintenance ease.
Specifications:
Motor | Primary Filter | Machine |
---|---|---|
Motors | Type Brushless motor | Filter Type Star filter | Dimensions 21.65x24.41 in |
Voltage | Frequency 120/60 V|Hz | Class EN 60335-2-69 M class | Height 51.29 in |
Maximum vacuum 92 inH2O | Media Antistatic polyester | Weight 99 lb |
Noise level-(EN ISO 3744) 72 dB(A) | Filter cleaning system Filter shaker | Bin capacity 11 gal |
Power 1.5 - 2 HP | Surface area 2,325 in² | |
Vacuum continuous use 92 inH2O | Spark-safe filter | |
Inlet 2.75 Ø in |
ATEX Conductive Hose and Tool Kit
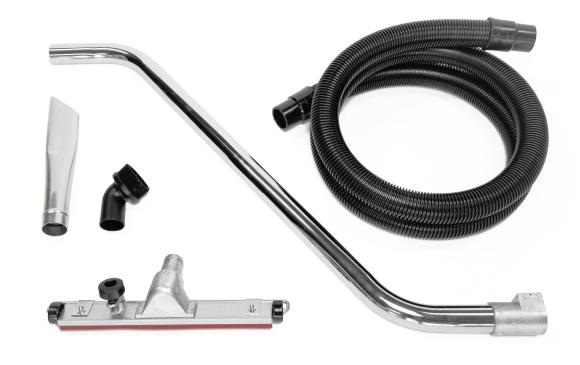
Each vacuum comes with basic starter package but you can upgrade to a more robust vacuuming hose and tool kit.
These come in 1.5" and 2" diameter depending on which vacuum.
We have a wide range of vacuum hoses, conductive tools and brushes, oil resistant hose and tools, and FDA approved for the food industry.